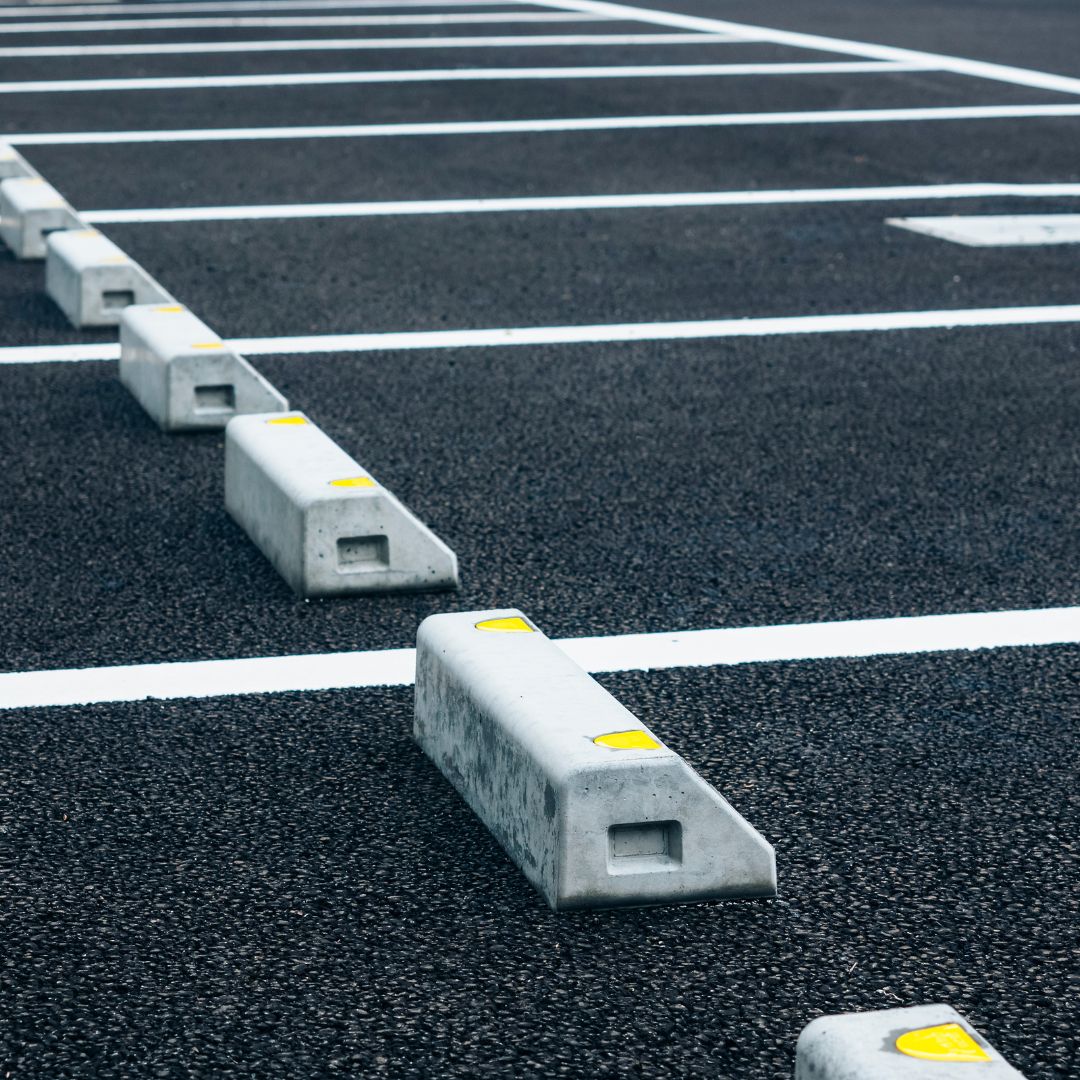
Commercial parking lots provide valuable parking space for customers, employees and visitors at many businesses. However, the asphalt surfaces that compose these lots can easily deteriorate over time when subjected to weathering, heavy vehicle traffic, and general wear and tear. Factors like freeze-thaw cycles in winter and constant weight on the asphalt from cars can accelerate damage. Left unchecked, cracks, potholes and other issues may develop and worsen and eventually impact the usability and aesthetics of the parking area.
For business owners, the parking lot is a major operational asset that sees daily use. Deterioration poses challenges like disrupting customer and employee parking or creating safety hazards. That’s why proper maintenance through periodic repairs is crucial for keeping the lot in good condition and the business running smoothly.
With this in mind, today’s post will focus on tips and recommendations for commercial parking lot repair. We’ll discuss the most common types of damages affecting asphalt surfaces, such as cracks and potholes, and recommend best practices for addressing each issue effectively.
If you’d like a quicker or more specific answer to your concrete repair questions, call the experts at TMC Engineering! If you’re in Southern California, we can help educate you on your problem and perform whatever repair is necessary. We’ve got an expert solution for your concrete or asphalt concern!
Commercial Parking Lot Repair: Understanding Common Causes of Damage
A commercial parking lot is a significant investment that requires diligent upkeep. As one of the most expensive business assets to maintain, parking lots can present ongoing costs if not properly cared for. By understanding typical causes of deterioration, proactive property owners can prevent issues and find targeted solutions to keep their lots in good working order for years.
Heavy vehicle traffic places tremendous stress on asphalt over time. Meanwhile, weather like freeze-thaw cycles during winter accelerate cracking and break down the surface more quickly. These and other environmental factors will naturally age parking areas when left unaddressed. However, comprehending such deterioration drivers helps identify early signs of damage for timely repair.
Here are some key tips: Catching small problems before they worsen results in simpler fixes that can substantially extend the lifespan of the lot. Knowledgeable repairs strengthen the pavement and forestall larger costs down the line. Lastly, methods ought to repair rather than replace wherever feasible. Overall, treating parking lots with regular maintenance tailored to their usage optimizes this important community resource to support business operations smoothly into the future.
How To Fix Common Issues in a Commercial Parking Lot
Some of the most prevalent problems affecting asphalt parking lots include cracks, potholes, and sinkholes. Here are some recommended repair methods for keeping these areas in good condition:
How to Repair Cracks in an Asphalt Commercial Parking Lot
For small cracks, consider crack sealing as a cost effective method. This involves routing out cracks less than 1/4 inch wide and filling them with a flexible sealant. It can be a DIY process but wider cracks may require professional routing and filling machines. As an alternative, crack filling involves cleaning cracks and filling them with a crack filler material like sand or gravel.
Whether caused by weathering or heavy vehicle use, cracks must be addressed promptly to prevent further deterioration if left unrepaired. Follow these steps for effective crack maintenance:
Step 1: Prepare the surface.
Thoroughly clean out debris and dirt from the crack using compressed air or water. Ensure any moisture is fully evaporated before proceeding.
Step 2: Seal thin cracks.
For cracks under 1/4 inch wide, apply a flexible sealant using a specialized routing tool to shape the crack edges first. Then insert the sealant with a high-pressure wand.
Step 3: Fill wide cracks.
Cracks 1/4 inch or wider should be filled. After cleaning, tightly pack the void with sand or gravel using a hand tamping tool.
Step 4: Follow-up with protective sealing.
Reapply a crack sealant annually after repairs are made. Regular sealing shields the repair from water damage that can undermine the fix over time.
By addressing cracks promptly according to their severity, commercial parking lots can remain sturdy for many years with minimum maintenance outlay. Don’t hesitate to contact a professional for any complex repair needs.
How To Repair Potholes in a Commercial Parking Lot
Larger depressions can form from water seeping into cracks over time. These should be patched promptly else they can lead to severe problems. You can read up on this in our post, “Why it is Important to Look Out for Potholes”.
For small potholes up to 3 inches deep, use cold patch asphalt. Simply clean the hole, add the patch, and compact it level with the surrounding surface. Deeper ones may need hot mix asphalt applied by a paving contractor.
Identifying and promptly filling potholes is key to maintaining a smooth asphalt lot over the long run. Follow these steps:
Step 1: Prepare the surface.
Clear out loose material from the pothole using a shovel and metal rake. Sweep thoroughly to remove all debris. This ensures proper bonding of new patch material.
Step 2: Prepare the edges.
For potholes over 6 inches wide, use an angle grinder to cut vertical sides at a 45 degree angle. This promotes stronger adhesion of the fresh asphalt.
Step 3: Fill the base layer.
Fill the hole about halfway with gravel then firmly tamp it level using a plate compactor. The gravel forms a stable underground base.
Step 4: Apply the patch asphalt.
Apply hot or cold patch asphalt, screeding it flush and smooth with nearby pavement. Act quickly before the mix hardens.
Step 5: Compact the patch.
Thoroughly compact the new patch with a roller or plate compactor, adding material if needed until level with surrounding asphalt.
With follow-up seal coating annually, these repairs provide an effective solution for maintaining safe, usable parking space. Catching issues promptly forestalls bigger problems down the road. You can read up on our post on “What Causes Potholes in the Road” for more information.
How to Repair a Sinkhole in an Asphalt Commercial Parking Lot
Seek help from a geotechnical engineer if a void forms under the asphalt. Filling may involve excavating around and under the void, then compacting stone and soil before repaving the area. Sinkholes indicate ground instability issues needing professional correction.
Sinkholes destabilize parking surfaces, so professional mitigation is essential. Follow these expert steps:
Step 1: Evaluate the site.
Contact a geotechnical engineer for a thorough site assessment. Understand the void’s cause and underground extent before repair.
Step 2: Excavate the site.
Dig beyond the sinkhole edges and beneath using a backhoe. The engineer can advise proper depth. Install bracing if soil stability requires extra support.
Step 3:Prepare the base.
In thin layers under 8 inches, backfill the void uniformly with compactable gravel or crushed stone. These stable materials form the new subsurface foundation.
Step 4: Compact the base.
Heavily compact each aggregate layer using professional-grade vibrating equipment. Achieve a 95% Proctor density rating for maximum support capacity.
Step 5: Resurface the patch.
Replace removed asphalt courses, sealing the finished patch annually like ordinary repairs. Periodic sealing protects the reinforced ground structure.
Early sinkhole attention with specialized engineering oversight yields secure, structurally-sound repairs for long-lasting commercial parking surfaces. Whereas, neglect can exacerbate issues exponentially.
With proper upkeep and repair, your parking lot can remain fully functional for many years.
In conclusion, keeping on top of maintenance and repairs is crucial for commercial parking lot upkeep. By understanding typical pavement deterioration factors and following these repair recommendations, property owners can effectively steward one of their most important operational assets. With proper upkeep following the techniques outlined here, asphalt parking facilities can serve businesses smoothly for many years to come.
Here at TMC Engineering, we have a deep commitment to delivering projects characterized by the highest safety standards as well as workmanship and client satisfaction. We aim to provide you with valuable informative content and insights related to the services our team of experts provides!
Whether you require asphalt paving, striping, sealing, or concrete work, we offer a full suite of transportation construction solutions. Because our team member’s experiences range from 20 to 33 years in this industry, we can work in all-weather conditions and have challenged them for our own confirmation. We invite you to contact us today for a FREE QUOTE. Let’s make quality projects together!