What Is AC Paving?
Paving is the process of creating a hard surface for transportation infrastructure like roads, driveways, parking lots, pedestrian areas, and more. It provides a smooth, durable surface that can withstand traffic loads and various weather elements. However, there are different types of paving materials and methods available based on the application and needs.
In this post, we will take a closer look at one specific type asphalt concrete or AC paving to understand what it is and what makes it unique compared to other forms of asphalt paving.
But, before you dive in , are you in Southern California and need your pavement construction done effectively and efficiently? Then, call the experts at TMC Engineering ! We’d love to help you with your gravel projects or any other concrete or asphalt work!
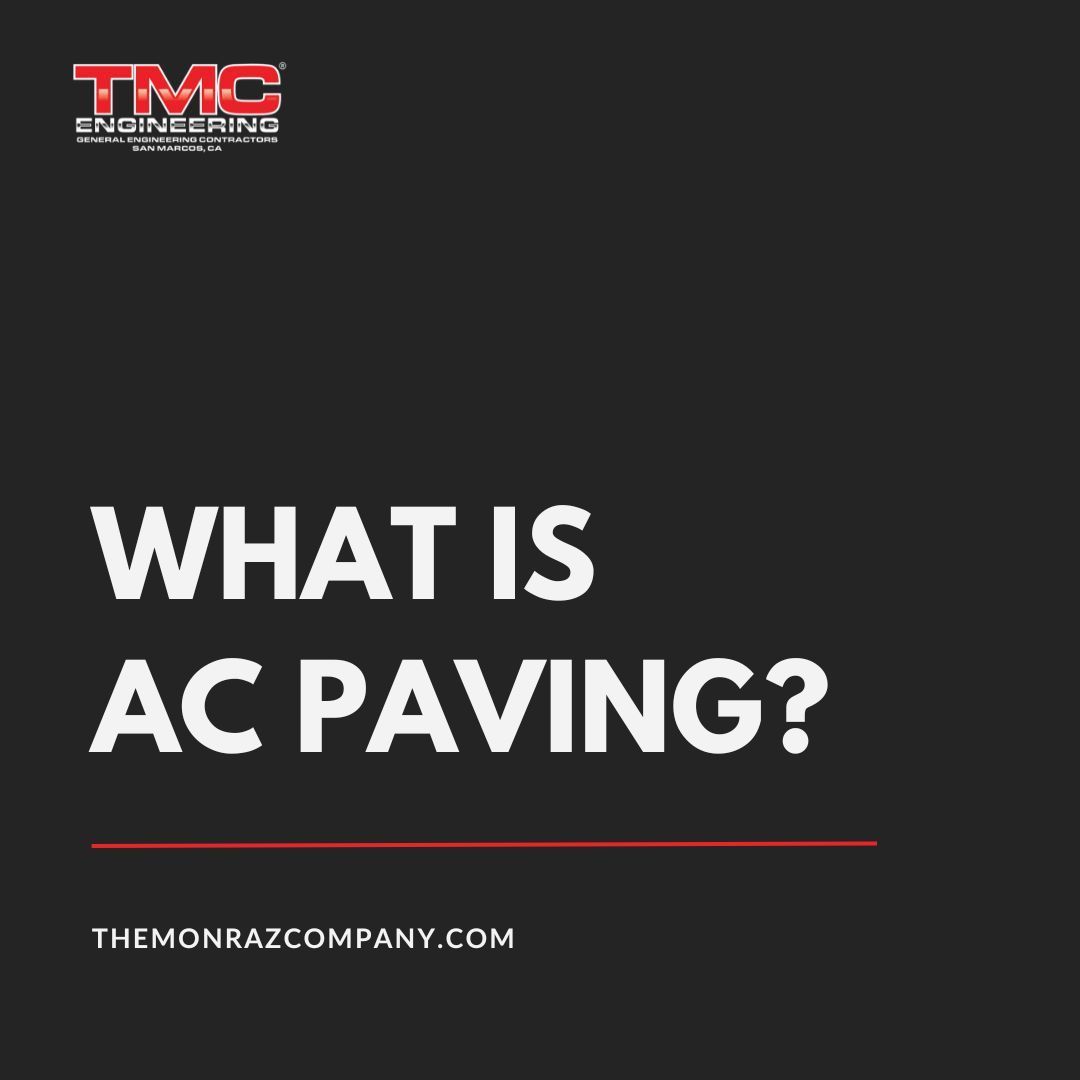
What Is AC Paving?
Asphalt concrete, more commonly known as asphalt or bitumen , is a composite material that hardens to become a very sturdy yet very flexible pavement upon application. It consists of an aggregate mixed with asphalt binder to shape asphalt mixtures or asphalt concrete mixes. The aggregate generally comprises crushed stone, sand, and gravel of varying sizes.
Asphalt binder is a black sticky liquid-like tar. When heated, it surrounds the aggregates and binds it together. This is where it gets the name , “asphalt concrete”, since it resembles normal concrete in constitution. When correctly blended, placed, and compacted such material forms a strong, waterproof surface able to take and distribute significant traffic and heavy loads!
So in summary, AC paving utilizes asphalt concrete , which is a versatile mixture of aggregates and asphalt binder that creates durable, long-lasting paved areas once hardened and set. Its ability to be engineered for various applications has made asphalt concrete one of the most widely used paving materials in the world.
What Is Asphalt Concrete Pavement Made Of?
Besides the aggregate materials varying by layer and application needs, asphalt concrete pavement relies on asphalt binder from residual oil processing to hold everything together. Here are all the ingredients needed to create asphalt concrete:
- Aggregates : Angular crushed stone, gravel, and sand of varying sizes and gradations for load spreading capability.
- Asphalt binder : A dark, sticky, petroleum-based material that coats aggregates, acts as glue when heated, and provides elasticity.
- Additives : Polymer modifiers, fibers, and anti-striping agents may be included in some asphalt mixtures to boost performance characteristics like flexibility in cold temperatures.
- Asphalt emulsions : Some mixtures use emulsified asphalt binders that allow lower temperature applications.
When properly designed, the asphalt binder coats and binds the aggregates through adhesive and film action. So that it forms a strong, waterproof, and flexible pavement structure upon compaction and curing.
Asphalt concrete pavement mixes incorporate aggregates and asphalt binder in ways that balance factors like load distribution, freeze-thaw resistance, and long-term maintenance requirements depending on the project needs. Professional contractors like us here at TMC Engineering ensure specific aggregate gradations and asphalt ratios are optimized based on an application’s functional demands and environmental exposures over the design service life.
How Does Asphalt Concrete Differ From Other Materials?
Asphalt concrete mixes can be prepared in various forms depending on temperature needs:
- Hot Mix Asphalt (HMA ) : Aggregates and heated asphalt binder are mixed at 300-350°F, producing the most durable pavements suitable for high-traffic roads and parking lots.
- Warm Mix Asphalt (WMA) : Uses additives to allow mixing and compaction at 230-304°F, reducing fuel usage and emissions versus HMA without sacrificing performance for low-moderate traffic applications.
- Cold Mix Asphalt : Aggregates bonded with emulsified asphalt at ambient temperatures below 104°F, ideal only for temporary repairs.
Asphalt concrete differs from rigid concrete pavement in several ways. It is more flexible and waterproof. The surface is easier to patch repair at a localized level. The existing pavement can be reclaimed after milling. All these features give asphalt mixes a benefit for nearly all types of pavement structures.
Beyond materials, asphalt concrete practices vary in their application and structural support. Some use asphalt emulsion surface treatments like chip sealing, which only uses a small amount of liquid asphalt to create a thin surface layer on top of the existing material, rather than building up load-bearing layers. While chip seals can serve as preventative maintenance seals, they do not provide the same total lifespan as full asphalt concrete pavement structures designed to bear structural loads.
In short, asphaltic or oil-based mixtures, defined by their production temperature, deliver flexible, durable, and reliably safe paving. This provides more capability than concrete or light surface treatments in most applications. This is because asphalt has pavement engineering designs and performance properties suitable for vehicle use. It offers mix design alternatives as well as environmental benefits through approaches like warm mix asphalt construction.
What Is Asphalt Concrete Pavement Used For?
- Roads, highways, bridges: The predominant use is for constructing roads, highways, interchanges, and bridge surfaces that experience heavy vehicle traffic on a daily basis.
- Parking lots: Asphalt concrete is ideal for large commercial and industrial parking lots, as well as smaller residential driveways.
- Airports: Runways, taxiways, and aprons at airports are frequently paved with asphalt concrete due to its strength and resilience under heavy aircraft loads.
- Bike and walking paths: Provides a smooth, accessible surface for cycling and pedestrian infrastructure.
- Sports facilities: Courts for basketball, tennis, and other sports often use asphalt concrete paving.
- Industrial facilities: Warehouse floors and areas with frequent forklift or heavy equipment use may opt for asphalt concrete surfaces.
Asphalt Concrete Pavement Layers
Subgrade
This is the native soil that serves as the foundation layer. Proper preparation like compaction and adding fillers improves the subgrade’s ability to evenly distribute loads without excessive settling.
Base Course
Usually composed of crushed aggregate like gravel or sand, the base course gives the roadway its initial load-bearing capacity and grade. It distributes stress across the underlying subgrade.
Binder Course
Finer crushed stone materials are used to create a denser, more flexible layer between the base course and wearing surface. It binds everything together structurally.
Surface Course
The top layer consists of the asphalt concrete wearing surface. Made from a graded aggregate mix and asphalt binder, it withstands traffic and protects lower pavement structures. Proper drainage and aesthetics are provided.
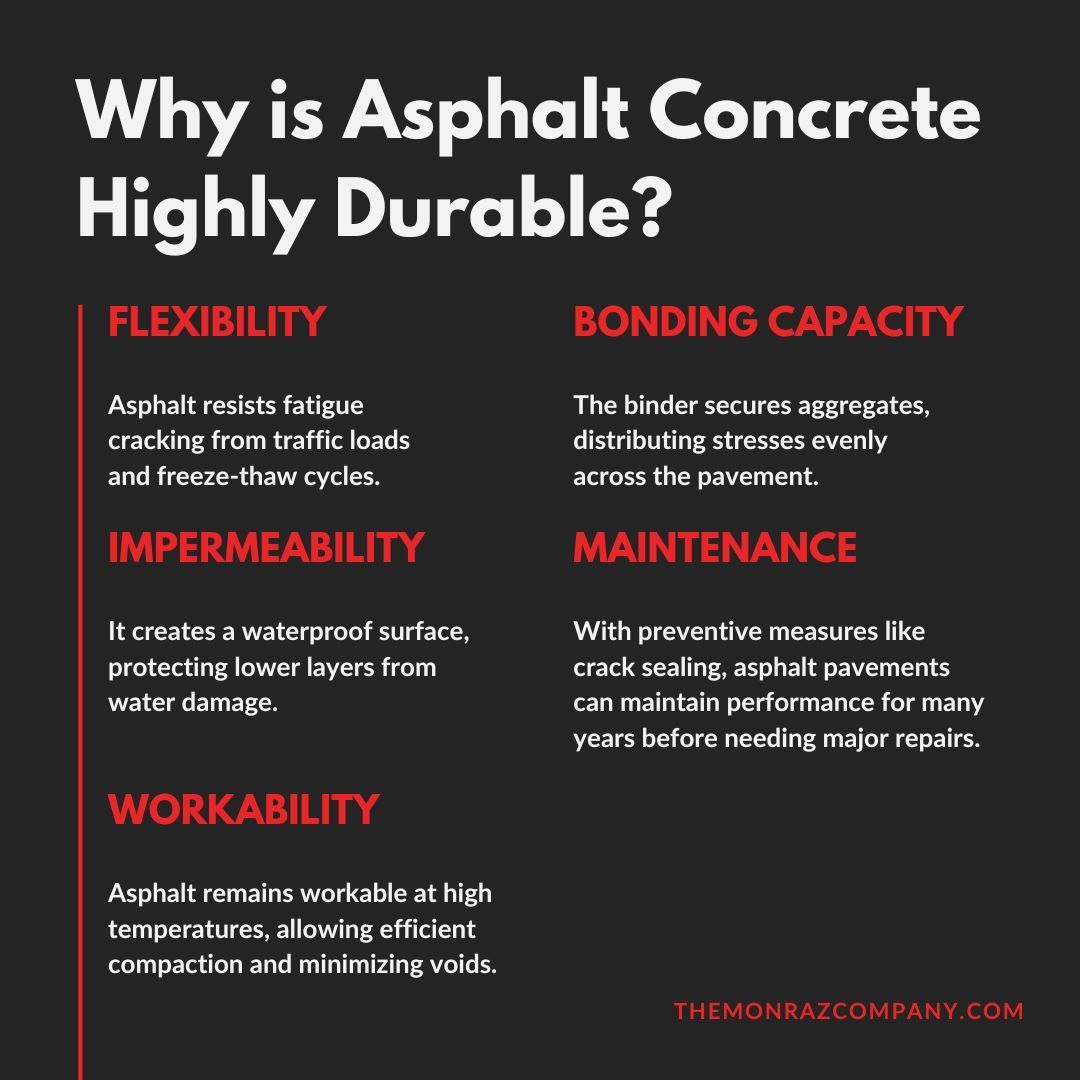
Why is Asphalt Concrete Highly Durable?
When installed correctly and with proper preventive maintenance, asphalt concrete pavements can last decades under heavy traffic conditions, withstanding repeated load and temperature variances. Several factors contribute to its robust durability:
- Flexibility : Asphalt binder provides resistance to prevent fatigue cracking from developing due to pavement stressors like traffic loads and freeze-thaw cycles.
- Impermeability : The asphalt binder and aggregate coating create a waterproof pavement surface protecting lower layers and subgrade from erosion damage caused by water infiltration.
- Workability : Asphalt mixtures remain workable at high temperatures allowing efficient compaction for maximum density and minimization of voids where water could infiltrate.
- Bonding capacity : The binder strongly bonds with aggregates, holding everything solidly in place and distributing stresses across the pavement structure as a cohesive unit instead of discrete pieces.
- Maintenance : In conjunction with preventive maintenance practices like crack sealing and thin surface overlays, asphalt pavements can maintain performance for decades before requiring thicker maintenance treatments.
If properly designed, mixed, installed, and preserved, asphalt concrete pavements can withstand many years of cumulative traffic and climate exposures, providing an overall cost-effective solution for surface transportation infrastructure. However, neglecting pavement construction standards or maintenance reduces lifespans and increases whole-life costs. With knowledgeable contractors, AC paving delivers longevity.
What Factors Impact Asphalt Concrete Performance?
Achieving successful asphalt concrete pavement relies on optimizing design and construction elements based on required outcomes and conditions:
- Climate/Exposure : Freeze-thaw cycles, extreme heat, precipitation intensity all necessitate tailored mixture properties to boost resilience against environmental damages over the design life.
- Traffic Loads : Higher traffic necessitate stiffer, thicker AC mixes with durable aggregate gradations and adequate asphalt content.
- Subgrade Quality : Poor soils increase the need for robust pavement structures built on top of quality, stabilized subgrades improved with appropriate techniques.
- Design Life : Pavements constructed to last 30 years will require different material compositions and structural layering than those meant for only 10-15 years of service.
- Construction Standards : Strict compliance with industry mix formulation techniques, temperature controls, installation practices, and quality assurance/control testing proves critical.
By professionally assessing how these factors impact the local application, asphalt concrete pavement designs are crafted to ensure long-lasting performance and functionality. Proper selection ensures you get the final pavement product you’re looking for!
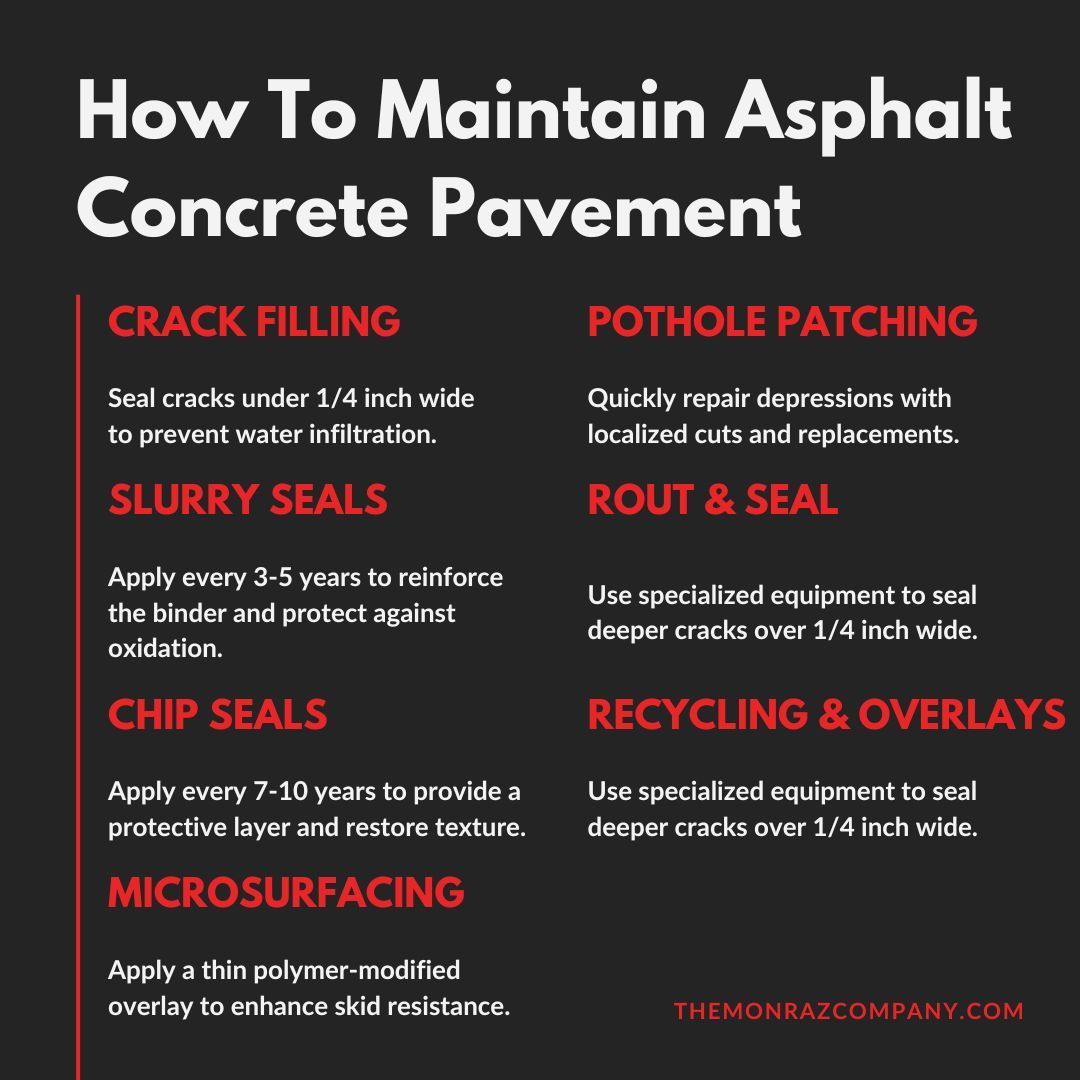
How To Maintain Asphalt Concrete Pavement
To maximize the service life expectancy of asphalt concrete surfaces, certain preventive maintenance strategies should be implemented on a routine basis:
- Crack Filling : Sealing cracks less than 1/4 inch wide prevents water infiltration and further cracking damage.
- Slurry Seals : Applications every 3-5 years reinforces asphalt binder and protects from oxidation effects.
- Chip Seals : Provides a protective wearing course and restores texture/friction when applied every 7-10 years.
- Microsurfacing : Renewable thin polymer-modified overlay and aggregate treatment enhanc es skid resistance.
- Pothole Patching : Quickly repairing depressions via localized cuts and replacements.
- Rout & Seal : Sealing cracks deeper than 1/4 inch width using specialized routing equipment.
- Recycling & Overlays : Milling and recycling existing aged asphalt into new AC mixtures as a cost-effective maintenance or rehabilitation technique once more extensive pavement deterioration occurs.
Proactive maintenance using techniques like these extends service lives, avoids costly reconstruction, and maintains smooth-riding asphalt surfaces. Neglect leads to accelerated aging, surface distresses, structural damages, and ultimately pavement failures requiring replacement treatments like full-depth reclamation.
A sphalt concrete (AC) can create durable pavement structures capable of handling heavy loads and years of use .
Proper design, quality construction, and maintenance yield long-lasting performance from asphalt concrete pavements. Customizing design and using high standards result in sturdy, resilient surfaces that can withstand heavy vehicle traffic of all kinds. With the right approach, asphalt concrete provides durable paved solutions for transportation.
Asphalt concrete pavements are easy to construct and maintain thanks to the expertise of experienced paving contractors. To learn more about asphalt pavement topics, check out our blog. You’ll find informative posts comparing concrete vs asphalt parking lots and other posts detailing different types of asphalt .
Here at TMC Engineering , we have a deep commitment to delivering projects characterized by the highest safety standards as well as workmanship and client satisfaction. We aim to provide you with valuable informative content and insights related to the services our team of experts provides!
Whether you require asphalt paving , striping, sealing , or concrete work , we offer a full suite of transportation construction solutions. Because our team member’s experiences range from 20 to 33 years in this industry, we can work in all weather conditions and have challenged them for our own confirmation. We invite you to contact us today for a FREE QUOTE . Let’s make quality projects together!
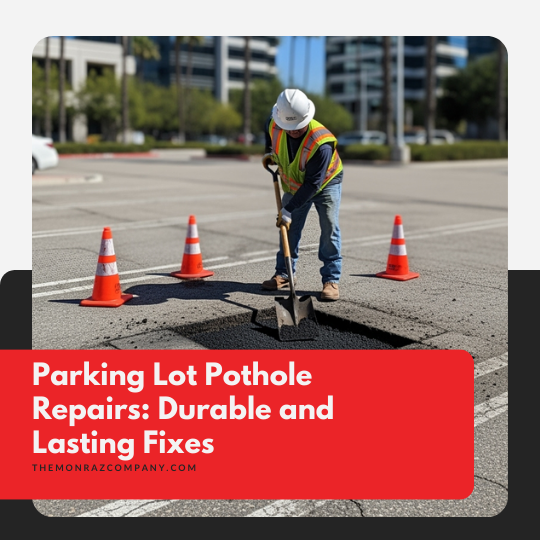