How To Repair a Concrete Parking Lot
Concrete parking lots endure a significant amount of wear from weather, traffic, and daily use over the years. Left unaddressed, small cracks and defects can progressively worsen, compromising the structural integrity and safety of the pavement. Beyond functionality, uncared parking lots with cracked or potholed surfaces may also negatively impact the appearance and value of commercial properties.
Proper maintenance through timely repairs is crucial to avoid potential hazards for both drivers and pedestrians that could result from cracked or uneven concrete surfaces. Potholes pose a tripping risk and can even damage vehicles if left to expand. Furthermore, an unseemly parking area with flaws may give an unprofessional impression and lower your property’s curb appeal.
With regular inspection and patching of cracks, as they first occur, expensive reconstruction can often be avoided down the road. Today, we will provide a guide on properly repairing concrete parking lots to keep them in tip-top condition. From thorough inspection of damage to selecting the right materials and techniques, following these best practices helps preserve safe, attractive parking infrastructure for commercial spaces.
Let’s get started with the first steps for maintaining a functional, well-kept concrete parking lot!
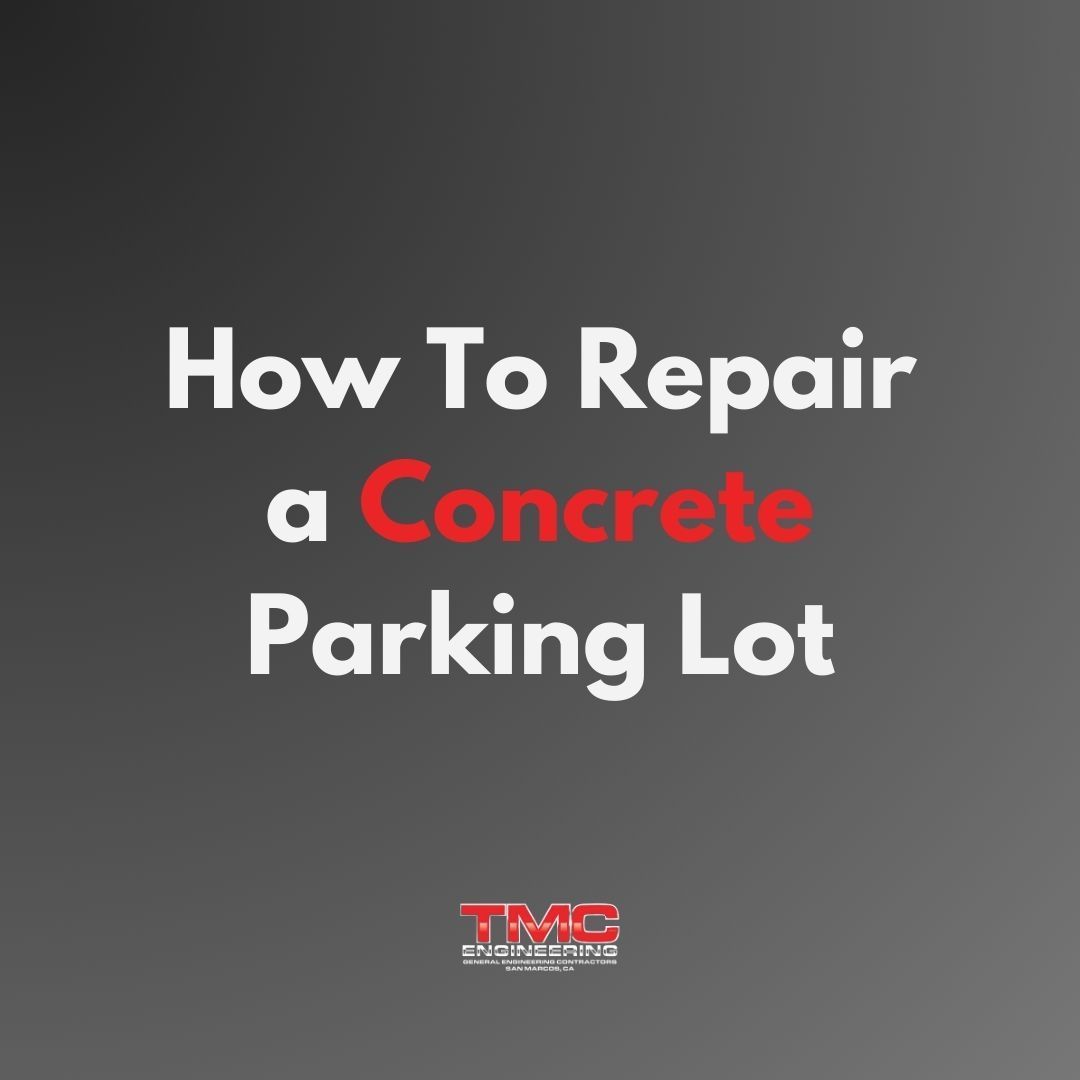
How To Repair a Concrete Parking Lot
Step 1: Inspect the damage.
The first step is conducting a thorough inspection to identify all cracks, flaws, and problem areas in need of repair. Make sure that you note the location, size, and severity of each concrete crack. Also pay attention to joints, edges, and any settlement or drainage issues affecting the pavement quality. This informs your strategic repair plan.
Step 2: Prepare the surface.
Before repairing cracks, potholes or other damage, the work area must be properly cleaned and prepared. Use sanders, grinders or scrappers to remove loose debris, dirt, oil buildup and anything else preventing bonding. Thoroughly sweep and suck up dust so the surface is structurally sound to receive new concrete.
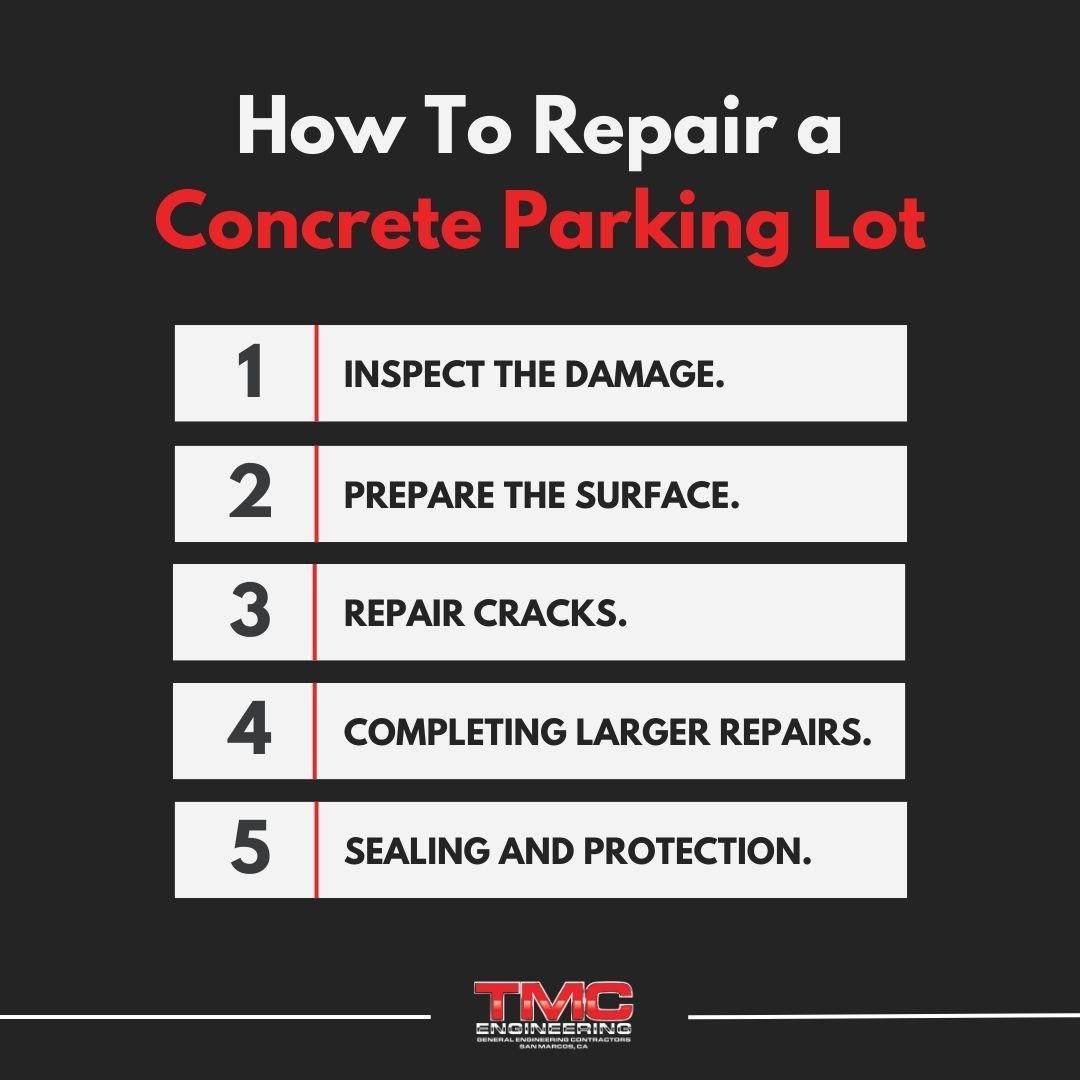
Step 3: Repair cracks.
Starting with minor cracks or flaws, use the appropriate sealant or filler matched to the width. For cracks up to 1/4”, use flexible concrete caulk or patching compound. Wider fractures on the other hand may require epoxy injection . Follow product instructions carefully for best adhesion.
Step 4: Completing larger repairs.
Deeper defects like faults or sinkholes require rebuilding techniques. For patching medium-sized sections, make square cuts and remove deteriorated material before replacing it with fresh concrete. Allow ample time to set and cure as specified.
Step 5: Sealing and protection.
Upon completion of all repairs, apply a high-quality concrete sealer. This guards against deicing salts, moisture penetration, and UV damage – all of which can accelerate the wearing of concrete parking lots. With regular reapplication, the sealer protects your investment.
Keeping up with routine concrete parking lot crack filling prevents minor issues from escalating into more serious and expensive repairs down the road. As outlined in the post “ When Can You Pour Concrete ”, maintaining integrity protects functionality for safe usage.
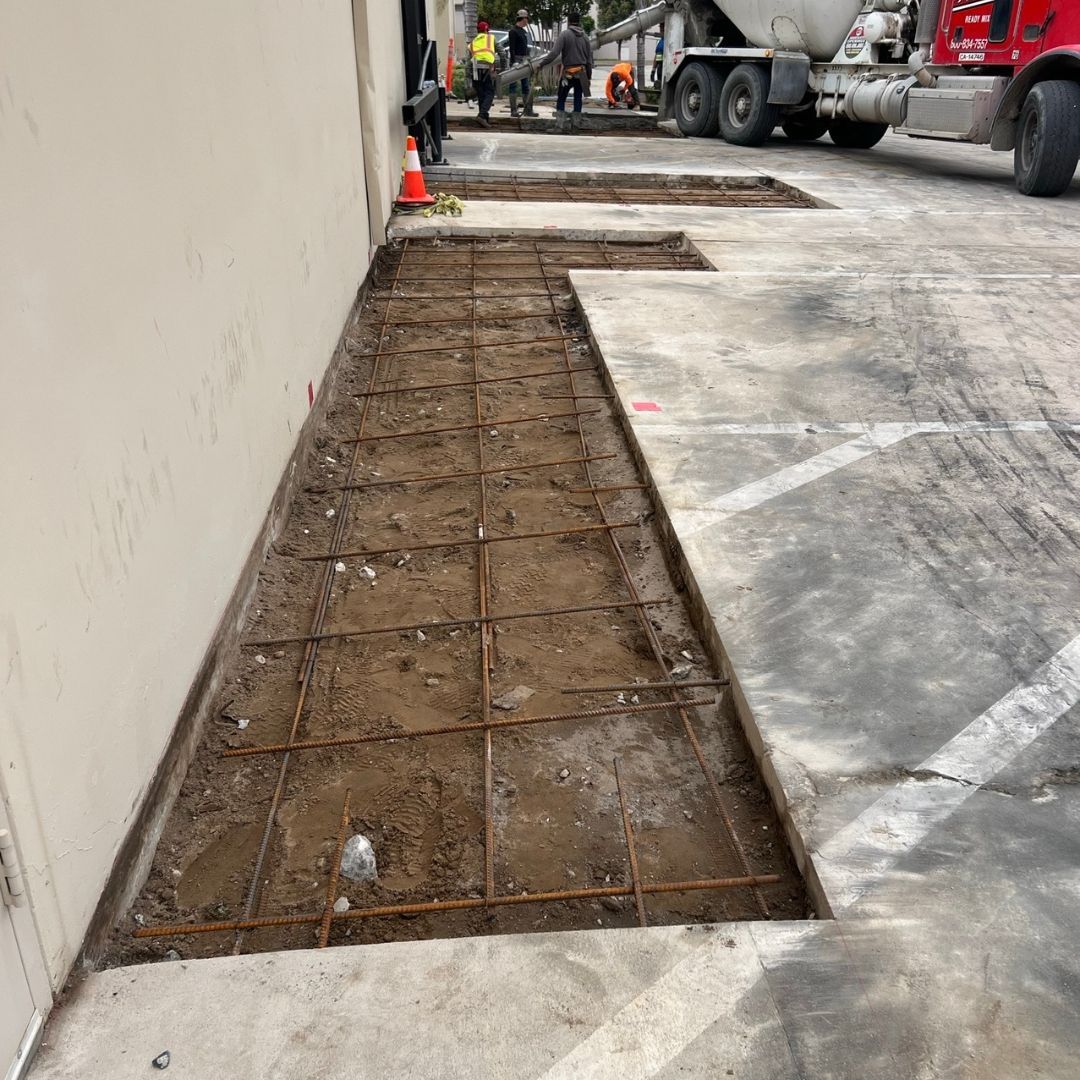
Repairing a concrete parking lot can go smoothly when you know what to do and the best people to do it.
In conclusion, taking a proactive approach to inspecting and repairing cracks, potholes and other defects is key to maintaining high-quality concrete parking lots over the long term. Small issues addressed promptly through the right repair methods keep bigger problems from developing down the road. Beyond functionality and safety, properly maintained lots provide curb appeal that can positively impact a commercial property.
With regular upkeep as recommended in this guide, concrete infrastructure can last for decades before requiring more extensive renovations. But repairing damage is only half the equation–protecting repaired areas through proper sealing extends the life of repairs. Combining reactive repairs with preventative sealing also ensures longevity in the long run.
Here at TMC Engineering , we have a deep commitment to delivering projects characterized by the highest standards for safety , workmanship, and client satisfaction . We aim to provide you with valuable content and insights related to the services our team of experts provides! Whether you require asphalt paving , striping, sealing , or concrete work , we offer a full suite of transportation construction solutions. Look no further–we’ve got all you need and more!