How To Fix Cement Steps: A Professional Guide
Cement steps are critical infrastructure for commercial properties. They withstand heavy foot traffic, harsh weather conditions, and the test of time. However, even the sturdiest cement steps eventually show signs of wear.
Cracks form, edges chip away, and surfaces become uneven, creating not just aesthetic concerns but genuine safety hazards and potential liability issues.
Deteriorating steps present significant risks for businesses. They can lead to customer injuries, compliance violations, and damage to professional reputation. Proper maintenance isn't just about appearance (though that certainly matters for business image). It's about ensuring your property meets safety standards while presenting a professional appearance to clients and visitors.
Today's guide covers effective methods for fixing cement steps at commercial properties. With the right approach, property managers can restore crumbling stairs while minimizing business disruption and controlling maintenance costs.
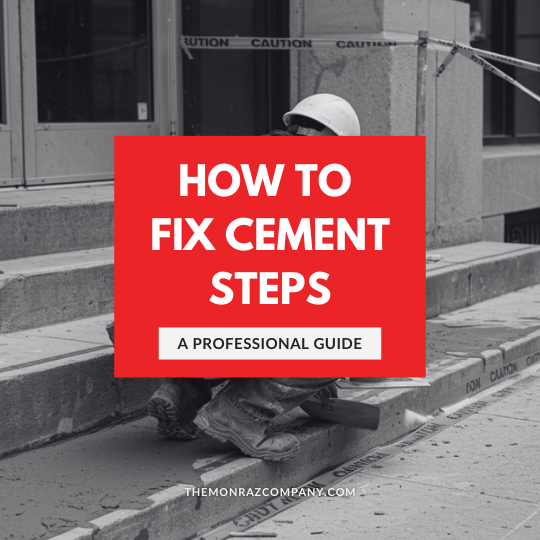
How To Fix Cement Steps
There are numerous reasons as to why commercial properties need to fix cement steps promptly. Building managers often notice hairline cracks spreading across steps, or entire chunks breaking off after freeze-thaw cycles. Whatever the specific damage, delaying repairs inevitably leads to more significant problems and higher costs down the line.
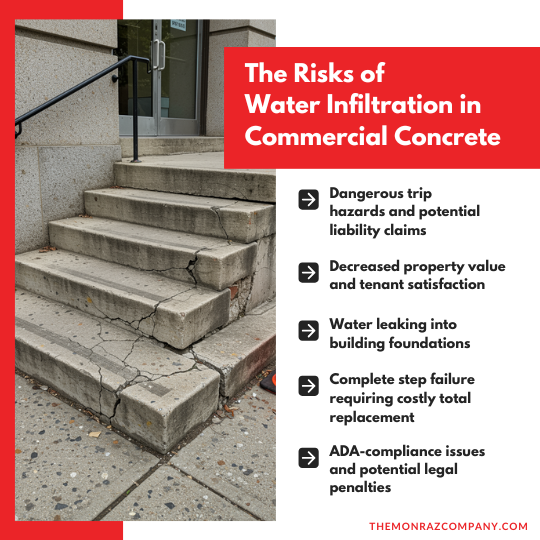
Water infiltration is particularly troublesome in commercial settings. When moisture seeps into cracks and freezes, it expands and forces the concrete apart. This makes what began as a small problem much worse. This deterioration can lead to:
- Dangerous trip hazards and potential liability claims
- Decreased property value and tenant satisfaction
- Water leaking into building foundations
- Complete step failure requiring costly total replacement
- ADA-compliance issues and potential legal penalties
Deferred maintenance often results in repair costs three to four times higher than early intervention would require. Smart property management addresses concrete issues before they escalate into major capital expenditures.
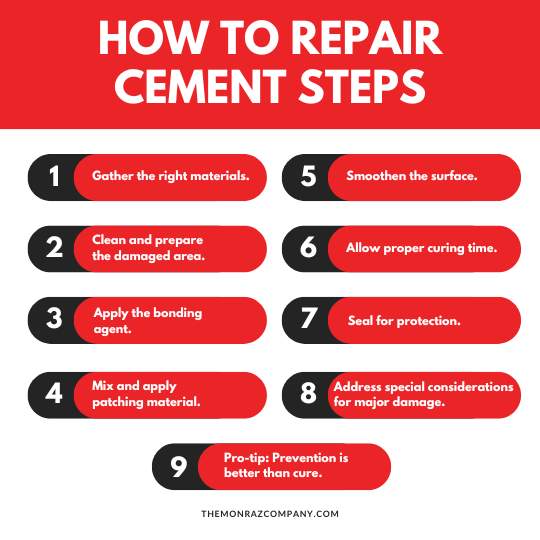
How to Repair Cement Steps
Before scheduling any cement repair work, facility managers must assess the damage accurately. Is the concrete surface just cosmetically damaged, or are there structural issues? The answer determines the appropriate repair approach and whether specialized contractors are needed.
1.Gather the right materials.
Commercial-grade repair projects require several professional tools:
- Protective gear (gloves, goggles, dust mask)
- Hammer and chisel or pneumatic chipping tools
- Industrial wire brush or grinding equipment
- Commercial pressure washer
- Professional-grade concrete patching compound
- Commercial concrete mix for larger repairs
- Professional trowels and floats
- Edging tools
- Commercial-grade concrete sealer
Investing in professional-quality materials significantly impacts repair longevity. Commercial properties require materials designed for heavy usage and extreme conditions. Lower-grade products may initially reduce project costs but often lead to premature failure and additional expense.
For the proper equipment to fit your concrete job, make sure to read our post:
"Tools for Concrete".
2.Clean and prepare the damaged area.
Repair success depends entirely on proper preparation. Professional contractors never apply new materials over compromised surfaces, as this virtually guarantees failure.
Begin by establishing a controlled work zone with appropriate safety barriers. Remove loose debris from the damaged area using appropriate tools. Chip away crumbling concrete until reaching solid material, creating a stable foundation for repairs. Thoroughly clean the surface with professional wire brushing equipment and rinse away all dust and particulate matter.
Maintenance teams that skip thorough preparation often see repairs fail within weeks, necessitating complete rework and additional expense. Commercial properties cannot afford such inefficiencies which means proper preparation is essential for durable repairs.
3.Apply the bonding agent.
For commercial-grade repairs to withstand heavy traffic, new concrete requires proper adhesion. Apply a professional-grade concrete bonding agent to the prepared area following manufacturer specifications.
This creates an adhesive surface that helps the patch form a permanent bond with the existing concrete. This step is particularly critical when repairing smooth, worn concrete surfaces where mechanical bonding is difficult to achieve.
4.Mix and apply patching material.
For smaller commercial repairs, professional pre-mixed patching compounds offer consistency and reliability. For larger areas, custom-mixing commercial-grade concrete provides cost efficiency.
When preparing concrete mixtures, professional application requires precise
water-to-cement ratios to achieve a consistency similar to thick mortar that remains workable without excessive fluidity. Commercial applications benefit from mechanical mixing for consistency. Apply the mixture to the prepared area, slightly overfilling to account for natural shrinkage during curing.
For structural corners or complex shapes, temporary forming systems help maintain proper dimensions and angles while the concrete cures. Commercial properties often require precise dimensions to meet building codes and accessibility requirements.
5.Smoothen the surface.
Use professional troweling techniques to smooth the surface, carefully matching the texture of surrounding areas for visual consistency. Professional edging tools create clean, defined lines along step edges that enhance both appearance and safety.
Avoid overworking the surface during finishing. Excessive troweling forces water and fine particles to the surface, creating a weakened top layer susceptible to premature failure. Professional finishers balance aesthetic appearance with structural integrity.
6.Allow proper curing time.
Professional concrete repairs require adequate curing time. Commercial properties must schedule repairs to accommodate curing periods. This is typically 24-48 hours before allowing light foot traffic, and a full 7-day cure before resuming normal commercial activity.
Maintain optimal moisture levels during curing by implementing controlled misting systems or applying curing compounds. This controlled curing prevents premature drying and potential cracking. This is particularly critical during hot or windy conditions when evaporation rates accelerate.
7.Seal for protection.
Once fully cured, apply commercial-grade concrete sealer to protect the repair investment. Professional sealers create an impermeable barrier against moisture infiltration the primary catalyst for concrete deterioration.
Commercial properties benefit from establishing a regular sealing maintenance schedule. You can work with maintenance every 12-24 months depending on traffic volume and environmental exposure. This preventative maintenance significantly extends service life and reduces long-term repair costs.
8.Address special considerations for major damage
Commercial properties with severely damaged steps often require comprehensive solutions beyond spot repairs. When structural integrity is compromised, professional assessment becomes essential.
For deep structural cracks in commercial foundation steps, specialized
epoxy foundation crack repair techniques provide superior strength and complete waterproofing compared to standard cement patching. This commercial-grade solution delivers exceptional longevity.
This specialized approach resolves persistent crack issues that conventional repairs cannot address. The epoxy system creates a permanent bond that withstands thermal cycling, vibration, and continued use.
9.Pro-tip: Prevention is better than cure.
While understanding how to fix cement steps is valuable, implementing preventative maintenance programs yields superior returns on investment for commercial properties:
- Implement winter maintenance protocols to prevent freeze-thaw damage.
- Schedule professional sealer application every 12-24 months.
- Establish regular inspection programs to identify and address small cracks before expansion.
- Train maintenance staff on proper snow removal techniques to prevent surface damage.
Industry statistics confirm that preventative maintenance programs reduce repair costs by approximately 70% over the lifecycle of commercial concrete installations. The minor investment in prevention delivers substantial long-term savings.
Professional concrete maintenance doesn't require specialized engineering knowledge just systematic inspection schedules and prompt attention to emerging issues. By implementing the techniques outlined above, property managers can maintain safe, functional, and professional-looking entrances while protecting their concrete asset investments.
If you’re in the San Diego area and need assistance to fix your cement steps, don’t hesitate to reach out to us at
TMC Engineering. We have the experience and expertise to assess your cement steps issues and provide the most suitable repair solution, including epoxy injection or other specialized techniques.
Contact us today for a free estimate on an inspection and repairs for your commercial building. Your structure’s longevity and safety depend on it.
Fixing cement steps is easy with the right tools and guide.
Concrete in commercial settings faces extraordinary demands but responds well to proper maintenance protocols. With appropriate care, commercial concrete steps can deliver decades of reliable service while maintaining compliance with safety standards and accessibility requirements.
For more information on how to deal with other issues on concrete, you can visit our blog. We have plenty of guides on numerous concrete issues, such as concrete parking lot repair, how to remove tar from concrete, and so on.
At TMCEngineering, we have a deep commitment to delivering projects characterized by the highest standards for safety, workmanship, and client satisfaction. We aim to provide you with valuable content and insights related to the services our team of experts provides!
Whether you require asphalt paving, striping, or concrete work, we offer a full suite of transportation construction solutions. Look no further—we’ve got all you need and more!